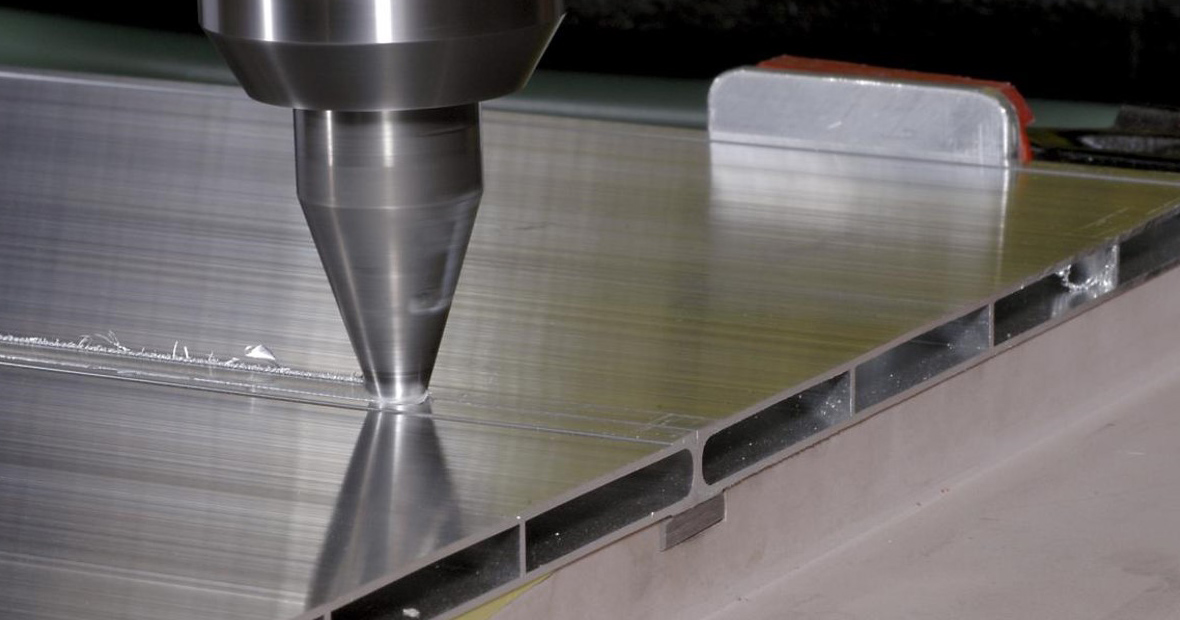
From its humble beginnings to the groundbreaking advancements of today, friction stir welding technology has undergone a remarkable transformation. This welding process, birthed from the innovative minds at The Welding Institute, has revolutionized metal joining, opening up a world of possibilities in various industries. Delving into the mechanics, one will appreciate the intricate process behind the transformation from frictional heat to a solid-state weld. The continual evolution of tools within this field, paired with the expanding material compatibility, has significantly enhanced efficiency and weld quality. This article will journey through the advancements in tools and techniques that have bolstered weld strength and quality, discuss the profound impact on the aerospace and automotive industries, and cast a light on the future innovations and emerging applications of this fascinating technology.
Birth of friction stir welding: the twi's revolutionary invention
The genesis of Friction stir welding technology at the Welding Institute (TWI) marked a significant milestone in manufacturing history, transforming traditional welding methods. A brief understanding of its creation reveals that the basic principles of friction stir welding rely on friction-generated heat. It's a unique advantage of this new technology, remarkably different from conventional welding techniques. The friction between the non-consumable rotating tool and the workpiece produces heat, softening the material, and allowing it to be stirred to create a joint. has had an influential impact on modern manufacturing industry, offering a more efficient, high-quality alternative to traditional methods. However, like any innovative development, it faced initial challenges. Overcoming these obstacles required innovative solutions, driving the technology's evolution. The scope of applications for this welding technique has grown exponentially, from aerospace to automotive industries, marking its dominance in new fields. This expansion stands as a testament to the practicality, versatility, and efficiency of this revolutionary invention by the TWI.
Exploring the mechanics: how fsw transforms metal joining
In the realm of welding technologies, Friction Stir Welding (FSW) has emerged as a revolutionary technique, transforming the way metals are joined. From its inception, this technology has evolved extensively, offering enhanced efficiency and superior weld quality.
Unveiling the process : from frictional heat to solid state weld
Understanding the basic principles of FSW involves comprehending the intricate balance between mechanical and thermal processes. The technique employs a non-consumable tool, made up of a shoulder and a pin, which is plunged into the workpiece. As the pin rotates and moves along the joint line, frictional heat softens the material, allowing it to be stirred together to form a weld without reaching the melting point. The shoulder plays a crucial role in this process, applying pressure to the workpiece and containing the heat within the work area.
Tool evolution in fsw : enhancing efficiency and weld quality
The evolution of FSW tools has significantly impacted the quality of the welded joints. Material selection, especially the use of different alloys including aluminium, heavily influences the strength and quality of the joint. The role of the pin and shoulder in joint formation cannot be overemphasized. The size, shape, and material of these components play a key role in determining the efficiency of the process, and the quality of the weld.
Material compatibility : expanding the use of fsw beyond aluminium
FSW has traditionally been used with aluminium due to its low melting point and excellent thermal conductivity. However, advancements have expanded its use to other materials, including various alloys. The effectiveness of FSW is largely dependent on the mechanical properties of the materials used. The selection of appropriate alloys plays a vital role in achieving high-quality, durable joints.
Advancements in fsw tools and techniques: enhancing weld strength and quality
Understanding the advancements in friction stir welding (fsw) tools and techniques is crucial in enhancing the strength and quality of welds. Over the years, the evolution of fsw tool materials has undergone significant changes, transitioning from conventional steel to high-performance alloys. This shift has resulted in a considerable improvement in the weld strength and quality. Alongside the advancements in tool materials, adaptive control techniques have been developed to optimize weld quality in the latest generation of fsw machines.
Furthermore, the speed of the probe's rotation has a direct impact on the microstructural properties and strength of fsw welds. Employing hybrid fsw tool strategies, which combine different probe geometries, can improve weld quality across varied thicknesses. Another factor contributing to the enhancement of weld strength and quality is the use of numerical simulation for designing optimized fsw tools.
Last but not least, progress in fsw tool cooling techniques has extended the tool's lifespan while maintaining high weld quality. By understanding and implementing these advancements, the strength and quality of friction stir welds can be significantly improved.
Broadening the horizon: fsw's impact on aerospace and automotive industries
Witness the transformation of the aerospace and automotive industries via the innovative use of Friction Stir Welding (FSW). This technology is responsible for manufacturing critical aluminium components in the aerospace industry, providing a marked improvement over traditional techniques, in terms of both strength and durability. The automotive industry has also seen a revolution in mass production, thanks to the efficiency of FSW, improving the resilience of vehicles and contributing significantly to their longevity.
Moreover, FSW has an undeniable impact on reducing production costs and carbon footprint within these industries. By refining the manufacturing process, a notable reduction in operational expenses has been recorded. Simultaneously, the lesser energy consumption of FSW compared to conventional welding methods has a positive effect on the environment. Aside from aluminium, the potential of FSW has expanded to include other alloys, diversifying its applications in advanced sectors.
Lastly, one cannot overlook the influence of FSW on innovation in the design and performance of aeronautical and automotive structures. Propelled by the capabilities of FSW, engineers are able to conceive and produce more efficient, durable, and cost-effective aerospace and automotive components. Truly, the impact of FSW on these industries is not just transformative but also a testament to the power of technological innovation.
Future frontiers: innovations and emerging applications of fsw technology
Staring into the future, a spotlight shines on the rising innovations and emerging applications of FSW technology. The manufacturing of lightweight, high-strength materials for aerospace applications is undergoing a transformation courtesy of Friction Stir Welding (FSW).
This technology, regarded as the next big leap in the manufacturing sector, brings advancements that are nothing short of extraordinary. One such advancement is the development of robotic FSW systems that deliver automated and precise welding in automotive assembly lines, enhancing both productivity and quality.
Another intriguing application of FSW is its growing use in the medical sector. Through a comprehensive study, it has been found that the tensile properties of biocompatible materials for medical implants and devices can be drastically improved with FSW. The technology is also breaking barriers with the development of portable FSW tools designed for on-site repairs in challenging environments like offshore platforms and space stations. The portability factor is a significant step towards equipping technicians with the best tools to perform their tasks efficiently and safely.
The future of FSW technology also looks promising in the realm of renewable energy. FSW has been applied in the fabrication of durable and efficient solar panel frames, leading to improved performance and longevity. Moreover, the integration of machine learning algorithms to optimize FSW parameters for customized material joining is an exciting innovation that is set to revolutionize the industry.